PID Control Loop Feedback System for Accurate and Precise Dosing Control
PID is a control loop feedback system used by Process Instruments, comprised of 3 components: Proportional, Integral and Derivative. PID is mostly used in industrial control systems, to continuously and automatically modulate a control output to achieve a desired setpoint.
Proportional (P)
This is the most commonly used component in system control, as it suits most applications without the need for Integral and Derivative control components. ‘P’ control is most effective when the process water is recirculated such as with a swimming pool. The main concept with proportional is that the further away the measured value is from the set point, the larger the controller output. This helps to achieve the setpoint and maintain the dosing throughout the water treatment process. However, in some processes where the measured parameter is lost to the process e.g. chlorine from a pool, the proportional control may approach the setpoint but won’t quite reach it. The difference between the setpoint and the achievable value is known as ‘droop’.
Integral (I)
Integral is used to eradicate ‘droop’ with a proportional controller or when the process water isn’t recirculated, such as on a water treatment plant. When Integral is used, the controller output is determined by both magnitude and duration of error. So small errors that occur over longer periods of time will trigger large responses. ‘I’ control therefore maintains the setpoint where there is a requirement to continually dose to reach the setpoint and maintain it.
Derivative (D)
Derivative uses the rate of change of deviation from the setpoint to predict future errors. As Proportional and Integral are extremely effective in process control, Derivative is rarely used.
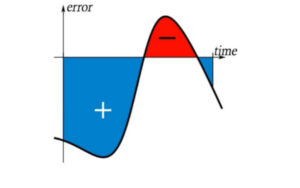
Integral Gain Graph
(The amount of time that the measurement parameter has been above or below the setpoint. ‘I’ is used when controlling process that require a steady setpoint, but dosing is never ‘off’.)
CRIUS®4.0 and CRONOS® controllers from Pi are often used to control chemical dosing in water treatment processes. This is because dosing via PID, as opposed to standard manual dosing or on/off relays based on thresholds can:
- Improve process stability
- Provide significant chemical savings (overdosing is heavily reduced)
- Reduce pump wear and tear (only used as and when necessary)
- Lower electricity costs
To learn more about Pi’s controllers, please click here. To read more about PID, please click here.
Related Posts
Total Alkalinity Analyzer Installed on one of Rio de Janeiro’s Biggest Drinking Water Plants
Online Total Alkalinity Analyzer, AlkaSense® Installed on one of Rio de Janeiro’s Biggest Drinking Water…
Online Turbidity Meter and Dissolved Oxygen Sensor Used by Chinese Distributors
Online Turbidity Meter and Dissolved Oxygen Sensor Used by Chinese Distributors Dr. Rob Paramore, Sales…
CRIUS® Technology: Uranium Enrichment and Process Safety
Urenco’s Long-Term Use of CRIUS® Technology: Uranium Enrichment and Process Safety Uranium is widely utilized…
Suspended Solids Controller Used in a Paper Mill
Suspended Solids Controller Used in a Paper Mill Measuring solids in the paper and pulp…