Analyzer to Pump - how controllers can interact with and control pumps
Pumps are almost ubiquitous in water processes; whether the pump is the main driver for water flow, is dosing chemicals, or is moving water around a sample line, there is (nearly) always a pump somewhere in the process. Often there are multiple pumps of varying sizes and specifications, making managing all of them a challenge for any operator. Did you know that… …today’s leading analyzers incorporate the majority of control algorithms a water process should need?
…water quality controllers can often accept fault signals from pumps to help keep your water systems safe and efficient?
…Pi’s CRONOS® and CRIUS®4.0 analyzers are the only analyzers that can be linked using SMART and DIGITAL communications to a Grundfos DDA pump? Analyzers and controllers will often interact with pumps for a number of different reasons:
Description: Some pumps can now be controlled using digital communications such as Modbus or Profibus. These are designed to be used directly from PLCs and they give operators distinct advantages over more traditional methods. A digital signal has longer range, has a signal cable for 2-way communication, and is able to transmit far more detailed information than a simple on/off alarm signal. An example of a pump with SMART and DIGITAL communication is the Grundfos DDA dosing pump with e-box add-on. The e-box provides a Modbus or Profibus connection for 2-way communication. The CRIUS®4.0 instrument controller from Pi is the only water quality analyzer capable of utilizing the full range of information available from the DDA pump. Information such as: total pump run time, pump pressures, volume pumped, and many more are now available to the analyzer. Error alerts can now be specific, telling operators exactly what needs to be done with their pump. This wealth of information can be useful in co-ordinating maintenance and increasing uptime for the pump and the system as a whole. All of this information can be stored, and data-logged, making the system very auditable. Normally all of this information would only be available to operators with access to a PLC, and a PLC engineer able to integrate the two systems, but the CRIUS®4.0 from Pi is a customizable controller that doesn’t need a PLC engineer to configure.
Control with the DDA e-box can also be extremely precise, with the pump more able to correct the pump output to very closely match the scale used by the analyzer. A pump being controlled by a 4-20mA scale, asking for 60% of the pump’s output, was more than a liter off the real value of 60% of the pump’s scale. This means that on a 0-30l/h pump, a pump controlled by a 4-20mA signal calling for 60% of the pump’s output would actually be pumping 19l/h, whereas a Modbus controlled pump would be pumping 18l/h. This difference is small but measurable, and over a pump’s lifetime would add up to a remarkable discrepancy in chemical. It’s likely that with longer cable lengths, on a real site, this discrepancy would increase. Advantages: The most precise control, excellent maintenance information, more uptime for processes. Disadvantages: Currently only available with Grundfos DDA pumps and Pi analyzers. Commonly used for: Large to very large systems, or 24hr systems where savings on chemicals and reduced downtime are amplified. Food systems in particular benefit from increased uptime and excellent auditability. There are many ways for analyzers to interact with pumps, and no single way is a ‘one size fits all’ solution. Whether you are retrofitting to an existing system, or designing a new plant with the latest in SMART and DIGITAL communications, Pi’s instrument controllers have you covered.
- Controlling chemical dosing – controlling a pump to dose a chemical into a system based on one or more measurements (e.g. chlorine residual and flow rate, please see the PID technical note for more information).
- Recirculation control – controlling a pump to manage the recirculation of a system (most commonly used in pools, please see the VSD Focus On for more information).
- Failsafe protocols – complex water systems can go wrong for any number of reasons, and analyzers can play a role in making those systems safer. Many pumps will output digital alarm signals when they detect a fault, alerting the dosing systems that something needs attention, and to stop dosing the chemical. Dosing into a water system which is not recirculating can lead to dangerous overdosing, and also wastes chemicals leading to increased costs.
- Duty rotation, or n+11 back-ups – in larger systems, pumps may be rotated in order to increase pump longevity or have a back-up system to rely on in the case of pump failure. Having a back-up, or n+1 system, can often reduce downtime significantly, and so is very useful in production lines where downtime can lead to large cost increases.
Power switching relay based control
Description: Power On/Off provides power to pumps when the analyzer needs the pump to be on, this can be 12-230V. Pumps are off and have no power when they are not pumping. Advantages: Cheapest and most universal method of control. Disadvantages: High pump and relay wear. Commonly used for: Small dosing pumps, pools, small water systems.Volt Free Contact (VFC) Control
Description: The pump is powered separately to the analyzer, and only begins to pump when a low voltage control circuit is closed. VFC can be used with thresholds or with PID and can be used as on/off control or pulse width/frequency. This means that the analyzer can mimic a flow meter’s ‘Pulse Control’. Advantages: Very commonly accepted by pumps and protects both the relay and the pump from high voltage surges. Disadvantages: Not as precise as analogue control, especially for non-recirculating systems. Commonly used for: Small to medium dosing pumps, pools.Analogue Control
Description: Either a 4-20mA or 0-10V is scaled to match the pump output, and is then used to control the pump rate. Advantages: Very precise control, even on non-recirculating systems. The pump is on all the time eliminating power surges and start-up fatigue. Disadvantages: Can only be used on pumps that accept analogue inputs. Commonly used for: Medium to large systems, large pool systems, any system where precise pump control is a necessity.SMART and DIGITAL control
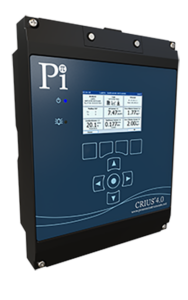
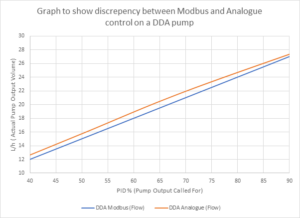
Graph to show discrepancy between analogue control and Modbus control on a DDA pump – the difference is very small but is measurable. This was measured on a real DDA pump in-house by Pi engineers.